Design from the inside out
Using NFC technology would require a user to be within 1.6” of each other in order to conduct a data transfer, resulting in a more personal human to human interaction. Simple voice activation would also allow for a user friendly and more personal human to machine interaction.
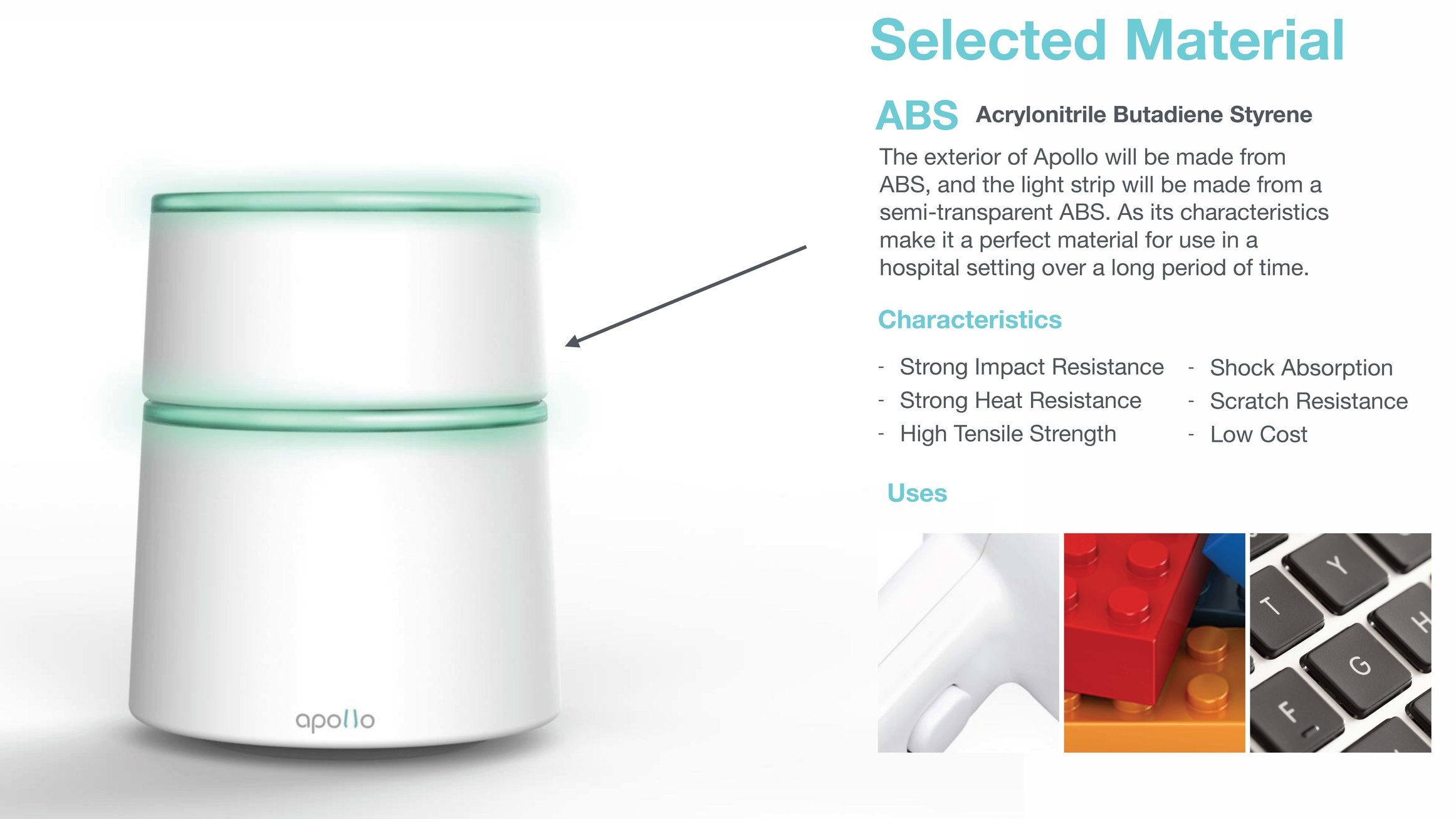
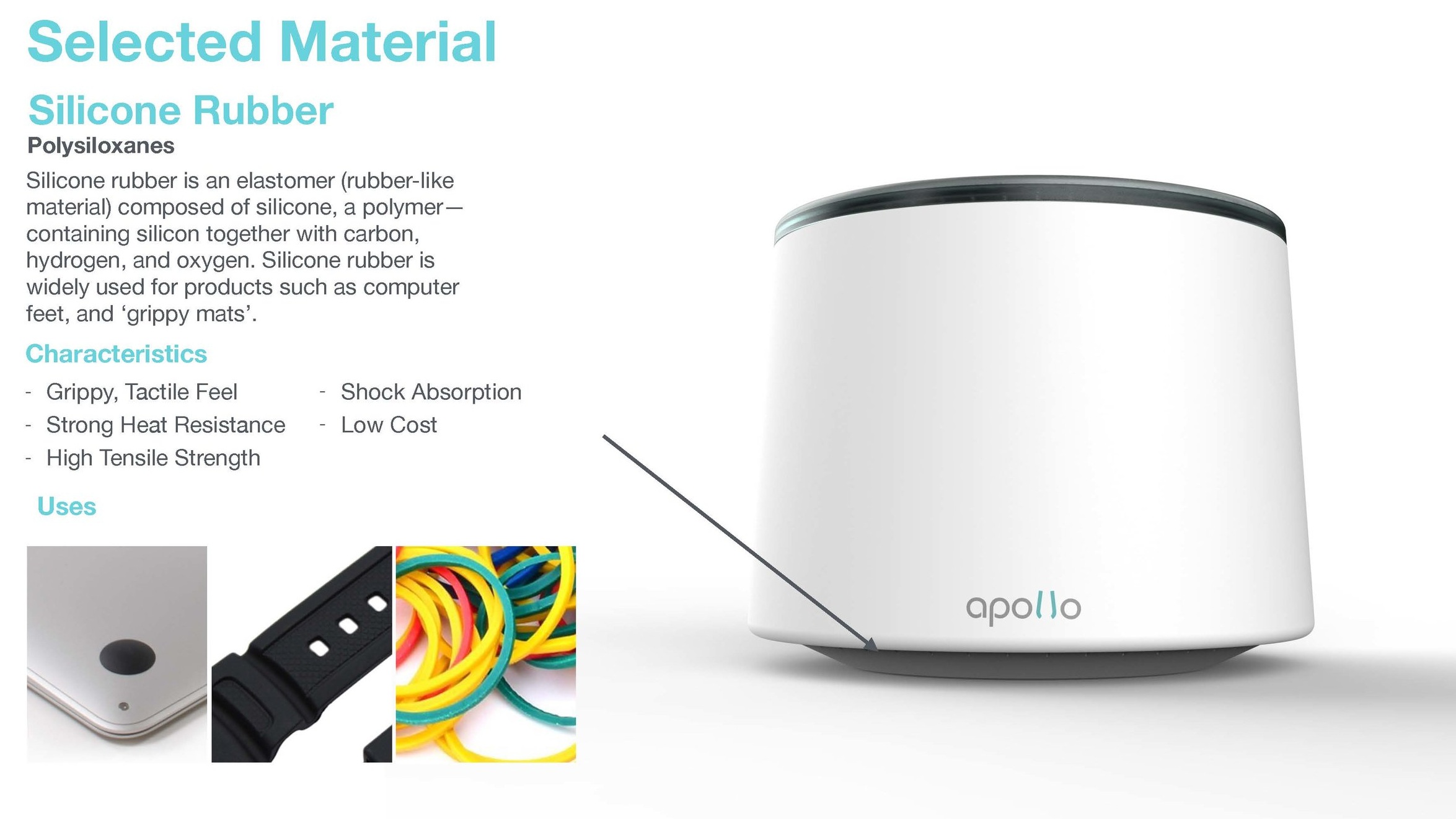
Manufacturing Processes
Plastic Injection Moulding
The plastic injection moulding process produces large numbers of parts of high quality with great accuracy, very quickly. With injection moulding, granular plastic is fed by a forced ram from a hopper into a heated barrel. As the granules are slowly moved forward by a screw-type plunger, the plastic is forced into a heated chamber, where it is melted. As the plunger advances, the melted plastic is forced through a nozzle that rests against the mould, allowing it to enter the mould cavity through a gate and runner system. The mould remains cold so the plastic solidifies almost as soon as the mould is filled. We would use plastic injection moulding to manufacture our exterior product.
Benefits:
Ability to create complex geometry and detailed features, both on a parts interior and exterior
High Efficiency
Strong, durable parts
Reduced costs in comparison to other manufacturing techniques
Ultrasonic Wielding
The connection process for Apollo. Ultrasonic welding is an industrial technique whereby high-frequency ultrasonic acoustic vibrations are locally applied to workpieces being held together under pressure to create a solid-state weld.
Benefits:
Visually appealing (Minimal to no seam)
Eliminates the need for screws or snaps
Fast turn around (depending on size of wield)
Very Strong for application